KISSsoft 2022 SP4 Win x64
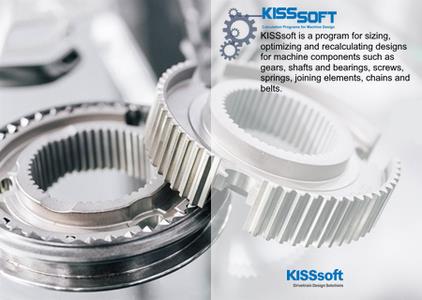
Free Download KISSsoft 2022 SP4 | 2.2 Gb
Languages Supported: Español, 中文, Deutsch, English, Français,
Italiano, 日本語, Português, Русский
KISSsoft, a part of multi-national Gleason Corporation, is pleased to announce the availability of KISSsoft Release 2022 Servicepack 4 is a modular calculation system for the design, optimization and analysis of machine elements.
Product:KISSsoft
Version:2022 SP4
Supported Architectures:x64
Website Home Page :www.kisssoft.com
Languages Supported:multilanguage
System Requirements:Windows *
Size:2.2 Gb
The KISSsoft Release 2022 SP4
General
SP 4 - Bearing names of some bearings in the database.
Some bearing names had hyphen/minus sign (-) replaced with zero (0), for example 70040B0XL02RS0TVP0L055 instead of 7004-B-XL-2RS-TVP-L055.
SP 4 - Material names with special character
Material names did not allow characters like <, <=, etc.
SP 4 - PDF resolution was set wrongly when exporting report to PDF
The line width of a graphic, embedded in a report, was wrong in case the report has been exported to PDF.
SP 4 - Required safeties not taken over
The required safeties were not taken over from calculation files of older releases.
SP 4 - System dynamics reports could not be shown.
System dynamics reports (e.g. modal analysis report in KISSsys) could not be loaded and shown.
Gears
SP 4 - Housing material did not always update correctly
The housing material for operating backlash did not update correctly if the material was selected using the plus button.
SP 4 - Housing material in tab operating backlash
Housing material (if set to own input) in tab operating backlash was not saved correctly to the calculation file. Results of the operating backlash calculation were not affected
Cylindrical Gears Rating
SP 4 - Calculation of tooth flank fracture and micropitting for double helical gears
Calculation of tooth flank fracture and micropitting for double helical gears was adjusted to properly consider force distribution. Changes in the safety factors of tooth flank fracture and micropitting are expected. Also difference in the effective tip relief is possible.
SP 4 - Carrier shaft file does not correctly consider deformation deflection in some cases
In cases where the carrier shaft file is specified for the face load factor or contact analysis, the direction of deformation was sometimes inverted.
SP 4 - Max. sliding velocity at the tip
Max. sliding velocity at the tip vga was not calculated correctly in case of multiple gear pairs. Also the sliding velocity of the second gear in a pair was not correct.
SP 4 - Maximum possible root radius coefficient in fine sizing
Maximum possible root radius coefficient was not set correctly in fine sizing when the option deep tooth form was used.
SP 4 - Pitting resisting power rating according to API 613 revised
The equation for the calculation of the pitting resisting power rating to API 613 was revised.
SP 4 - Planetary contact analysis graphics show same results for each planet
The graphics of the contact analysis for planetary gears showed the same results for each planet when changing the planet number.
SP 4 - Using US customary units in fine and rough sizing
Data was not converted correctly if rough, fine and modification sizing was used with US customary units.
Cylindrical Gears Contact Analysis
SP 4 - Evaluation area option in contact analysis settings caused prevented graphics from being shown.
Reducing the evaluation area options in the contact analysis prevented certain graphics from being shown and in some cases caused a crash.
SP 4 - False torsion warning was shown when calculating face load factor according to Annex E in modules with more than one pair.
Warning messages related to the torsion are shown erroneously in modules with more than one pair when calculating the face load factor according to Annex E. One message read "Torque is not taken into account" and another recommended the user to set the torsion direction 'From shaft calculation'. These messages were shown regardless of torsion settings.
SP 4 - Fine sizing crashed when contact analysis calculation was done
In some cases contact analysis in fine sizing of cylindrical gears stopped working.
SP 4 - Partial load wt for contact analysis calculation in fine sizing for planetary gears
Partial load wt for contact analysis calculation for planetary gears was not considered correctly in fine sizing.
SP 4 - Planetary CA report display of manufacturing deviations even if not considered
The contact analysis report displays of any previously entered manufacturing deviations from the factors tab even if not considered in the contact analysis tab.
SP 4 - Planetary CA resultant load factor now uses maximum dynamic factor
Planetary CA resultant load factor now uses the maximum dynamic factor between sun/planet and planet/ring if the dynamic factor is considered.
Cylindrical Gears Geometry
SP 4 - 3D gear geometry in Inventor or Solid Works
In some cases the 3D model of the gear could not be generated in Inventor or SolidWorks.
SP 4 - Tip form diameter dFa calculation with semi-topping tool and tip alteration of the gear
In some special cases (semi-topping tool, positive tip alteration on the gear), the tip form diameter dFa was not calculated correctly.
Bevel Gears
SP 4 - 3D bevel geometry with modified blank caused an error in special cases
3D bevel geometry with modified blank caused an error when the option "Use updated approach for the flank line modification calculation" is selected.
SP 4 - 3D model of internal bevel gear
The 3D geometry of an internal bevel gear is now working correctly. The shaft editor and 3D viewer in shaft calculation module are also fixed accordingly.
SP 4 - Measurement grid error of bevel gear
The measurement grid was wrong when the setting "Use updated approach for the flank line modification" is activated.
SP 4 - Small correction in the bending moment arm calculation
For bevel gears with xsm ≠ 0, the calculation of the bending moment arm hFa was corrected. Only minor differences are expected.
Face Gears
SP 4 - Calculation error in the face gear for shaft angle not equal to 90 degrees
Some of the geometries such as the height of the gear body and the assembly distance were wrong for the face gear with the shaft angle not equal to 90 degrees.
SP 4 - Measurement grid of face gear fixed
The measurement grid of a face gear with a shaft angle not equal to 90 degrees and with an axial offset was wrongly disabled since the release 2021 SP3. Now it's enabled again.
Shafts
SP 4 - Forced response graphic could not be exported as curve
Fix in the export of Forced Response graphics as curves.
Bearings
SP 4 - Bearing rating life in revolutions in the special report for classic bearing calculation
Rating life in revolutions (L10 and Lnm) in the special report for classic bearing calculation were always calculated by considering nominal bearing speed. This resulted in wrong results when considering load spectrum with different rotating speeds.
SP 4 - DIN 31652 with ring nut didn't use the half width to define the lubricant flow rate Q1
For the calculation according DIN 31652 for with ring nut arrangement uses the half width to define the lubricant flow rate Q1. Until now, the whole width was used.
SP 4 - Fine sizing of internal geometry bearing in module Rolling bearing ISO/TS 16281
After performing fine sizing of internal geometry bearing in module Rolling bearing ISO/TS 16281 accepting a solution didn't work.
SP 4 - Message when shaft definition of connecting bearings is inverted
When connecting rolling bearing had wrong (i.e. inverted) definition for inner and outer shaft and bearing calculation did not consider bearing stiffness calculation according to ISO/TS 16281 wrong message about transition and interference fits was displayed.
SP 4 - Roller length in case of proprietary rolling bearing internal geometry data
In case of using proprietary rolling bearing internal geometry data, the roller length and the positions of roller sections are no longer shown in the rolling bearing reports and in the graphics. Instead, only the numbers of rolling element sections are shown.
SP 4 - Show custom (OTHER) and RKB rolling bearings in selection drop-downs for existing calculation files
KISSsoft will now show custom bearings (manufacturer=OTHER) and RKB bearings in bearing selection drop-downs by default also for calculation files made with KISSsoft releases prior to 2022. In case of existing older calculation files until now these two manufacturers had to be explicitly turned on in module specific settings.
SP 4 - Wrong comments for bearing in module Rolling bearing ISO 281, ISO 76
In case when more than 1 bearing was chosen in module Rolling bearing ISO 281, ISO 76, in some cases bearing 2 had wrong comments in the user interface.
SP 4 - Wrong roller length when using spherical roller bearings with TIMKEN cloud services
When calculating TIMKEN spherical roller bearings and using TIMKEN cloud services the roller length was multiplied by 2.
Shaft-Hub Connections
SP 4 - Facewidth sizing for spline-hub connections
Sizing of the facewidth did not work correctly for spline-hub connections.
Bolts
SP 4 - Average achieved tightening torque wasn't always correctly calculated
Average achieved tightening torque wasn't always correctly calculated, in some cases the value wasn't in the middle of the maximum and minimum.
SP 4 - Bolt length sizing improved
Bolt length sizing gave in some cases strange results, the sizing is improved now. Proof of Strength with Local Stresses
SP 4 - Material selection fixed
The material was not read from the data base correctly. Some of the material data were different, that can have influence on the static utilization results. Load Spectrum Generator
SP 4 - Time series to LDD calculation in KISSsys
Time series to LDD calculation in KISSsys was not running when KISSsys was installed on the server.
Tolerance Chains
SP 4 - Tolerance calculation wrong in some cases
In some cases, the tolerances were wrongly calculated.
FEM Calculations
SP 4 - Request confirmation from the user before overwriting the stiffness matrix of a gear body
When using the gear body calculation to generate a reduced stiffness matrix, the confirmation of the user is now requested whenever the selected stiffness matrix file already exists.
SP 4 - The density of the gear body material is not saved correctly with the file
When using an "Own input" material definition for the gear body, the density of it was not saved correctly with the calculation file. The calculation is performed correctly.
CAD-Interfaces
SP 4 - Interface to Siemens NX2212
Interface to Siemens NX2212 added.
SP 4 - SolidWorks: To cutout the tooth from a cylinder for helical gears with an helix angle bigger than 14° was not always working
To cutout the tooth from a cylinder for helical gears with an helix angle bigger than 14° and helix left hand was not always working.
Forced Response Shafts
SP 4 - Rotating speeds of non-reference shafts in Campbell diagram and Forced response
When calculating Campbell diagram or Forced response with more than 1 shaft the calculation didn't consider correct shaft speeds of non-reference shafts if own shaft speed was set for these shafts.
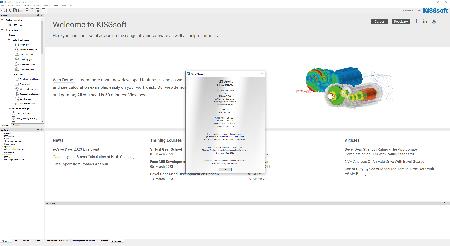
KISSsoftis a modular calculation program for the design, optimization and verification of machine elements according to international standards. The individually customized software packages for a wide variety of applications guarantee tailor made solutions and the integration to all common CAD software complete the product.
TheKISSsoft release 2022provides numerous innovations - amongst others, in order to include the tooth fatigue limit in the verification, the information can be generated from time series. The determination of load spectra from time series (torque-speed-time) is now an independent module ("Load spectra"), which can be used to calculate load spectra for gears and for shafts/bearings. In addition to detailed reports, many graphics are now available for displaying the results. Positive and negative torques result in alternating load in the tooth root. The Rainflow method is used to de-termine the number of cycles with a shift from high to low torque. Based on this, the alternating bending factor YM, according to ISO 6336-3 (extended), is determined additionally for the load spectrum in the gear calculation of each element.
Web Demo KISSsoft Release 2022, English, June 15th, 2022
Learn more about how the enhancements in KISSsoft Release 2022 will make your gear design more efficient and refined. We are also excited to show KISSsoft in a modernized look.
KISSsoftis part of multi-national Gleason Corporation, as a wholly owned subsidiary. KISSsoft AG directly serves various industries and customers globally. The most powerful source of ideas are our customers: Suggestions and recommendations from innovative companies throughout the world have all contributed to the further development of our software, ensuring that KISSsoft, KISSsys as well as KISSdesign are always at the forefront of technology.

Links are Interchangeable - Single Extraction
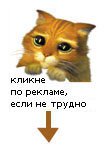