CAMWorks 2023 SP3 Win x64
- ПРОГРАММЫ
- 2-08-2023, 13:23
- 150
- 0
- TUTBB
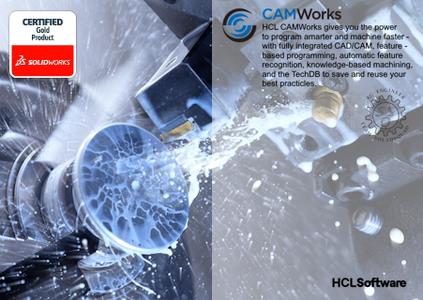
Free Download CAMWorks 2023 SP3 | 1.6 Gb
Languages Supported: 中文 Simplified, 中文 Traditional, Français, Deutsch, Italiano,
日本語, Polski, Português-Brazilian, Русский, Español, Türkçe, 한국어, Čeština
Owner:HCL Technologies (HCL)
Product Name:CAMWorks
Version:2023 SP3 build 2023/0712 (12-Jul-2023)
Supported Architectures:x64
Website Home Page :www.camworks.com
Languages Supported:multilanguage
System Requirements:Windows *
Size:1.6 Gb
The HCLSoftware development team is pleased to announce the availability ofHCL CAMWorks 2023 SP3is an intuitive, feature-based CAM software that helps to increase productivity using best-in-class technologies and adaptable automation tools to maximize CNC machining efficiency.
1. CWR-2134 CSR-22948 Toolpath For the specific Mill part, when the 3 Axis Mill toolpath generation method is set to 'Advanced', the quality of the Z-level toolpath that gets generated is very poor when the applied corner type parameter is set to "Round". Thedifference is observed in entire toolpath instead of only corners.
2. CWR-2127 CSR-22658 Toolpath For the specific Mill part, when the 3 Axis Mill Toolpath generation method is set to 'Advanced', the quality of its Pencil Mill toolpath is not as good as the toolpath generated using the 'Previous' method. (All the parameters are kept similar when generating the toolpath using both the toolpath generation engines.)
3. CWR-2116 CSR-22517 Toolpath For the specific part, when the 3 Axis Mill Toolpath generation method is set to 'Advanced', the toolpath that gets generated for Flat Finish operation gouges the partwhen the Mach deviation is set to 0.1mm.
4. CWR-2063 CSR-20817 Toolpath When the 3 Axis Mill Toolpath generation method is set to 'Advanced', the Z level toolpath with the 'round type corner' makes incorrect moves where the tool diameter is bigger than the corner radius. This results in the tool noncutting area gouging the part. When compared to the toolpath generated with the 'Previous method', the toolpath quality of 'Advanced' method is poor.
5. CW-122086 CSR-23533 Setup Sheet The *.xml file output for the Setup Sheet does not output the parameter "Toolpath Center" under the NC tab of Operation Parameters dialog box for the Contour Milloperations.
6. CW-121902 CSR-23435 CSR-23490 Post For any assembly file having multiple part instances, when the 'Grid pattern' or 'Feature instances' option is used for sorting instances, the NC code that gets generated is incorrect.
7. CW-121452 CSR-23301 Simulation When running the simulation for any toolpath having a 2.5 Axis operation immediately after a Multiaxis operation, then the tool orientation shown in the simulation is incorrect
8. CW-121410 CSR-23256 System When trying to open the specific Mill part (for which thedata was last saved in CAMWorks 2022 SP1) in a later version of CAMWorks, it causes the CAMWorks application to crash.
9. CW-121137 CSR-23178 Toolpath For the specific Assembly, when its Contour Mill operation's Leadin Amount is changed to 10%, an error indicating that the Leadin/out doesn't have a linear moveand will therefore not work for Cutter Compensation gets displayed. This message is incorrect as there is a leadin and leadout move to the center of the hole.
10. CW-121136 CSR-23178 Toolpath For any Mill part, when the Leadout contains an arc, a Leadout line, and a move to the center, it is observed thatthe CUTCOM/OFF NC output is incorrect.
11. CW-120888 CSR-23025 UIF For Turn Finish operations, when the Undercut option is checked under the Turn Finish tab of Operation Parameters dialog box, if this dialog box is closed and reopened, it does not retain the check placed in Undercut checkbox.
12. CW-120830 CSR-22990 System When user attempts to open the specific part file in CAMWorks (which is loaded as an add-in within the SOLIDWORKS application) it causes SOLIDWORKS to crash. Also, an error message, "CAMWorks data could not be restored. Please consult your documentation for details."gets displayed.
13. CW-120437 CSR-22825 Post With UPG-2 user interface, for a Mill-Turn machine, when inserting any command using the available buttons forcanned Rough ID/ OD under Turn section, an exception error gets generated.
14. CW-120405 CSR-22789 Translation In Japanese language version of CAMWorks, the text string "Convert to 5 axis" under the Advanced tab gets displayedonly partially.
15. CW-120315 CSR-22725 Operation In CAMWorks, for the specific part file, when the operations are swapped from one tool to another toolwithin the Tool tree node, the Leadin/ Leadout moves for that operations do not get recalculated dynamically. Theuser needs to edit and preview the operations manually.
16. CW-120281 CSR-22738 Toolpath For the specific part model created in an older version of CAMWorks, the Rest Machining has been defined using an STL file. When opened in a newer CAMWorks version, after re-specifying the STL file, toolpath generation fails and a "0" error is displayed within the Process Manager.
17. CW-120270 CSR-22735 Toolpath During Thread Milling, depending on whether "Gouge check" is set to On/Off or, when using User Defined LeadIn/Out, the linear leadout move to the center of the hole is a rapid move and not a feed move.
18. CW-120084 CSR-22728 Translation In Polish language version of CAMWorks, the text string "Retract dist." for turning operations under the NC tab of Operation Parameters dialog box is incorrectly translated.
19. CW-120077 CSR-22453 Toolpath For the specific Thread Mill operation, when the user defined Leadin/ Leadout is applied, the toolpath that getsgenerated gouges the part.
20. CW-120060 CSR-22680 API New API that enables post processing of "Probeoperations" required.
21. CW-119868 CSR-22636 Toolpath For the specific Mill part, when using the "Advanced"method to generate an Adaptive Roughing toolpath withHog Nose tool, an overcut is observed while runningsimulation for this feature. If the "Previous" method is used to generate the toolpath without changing the other parameters, then correct toolpath gets generated.
22. CW-119741 CSR-22660 Toolpath For any Mill part model, when a toolpath is generated for the Cleanup pass on Round islands, the Leadin/Leadout moves do not get generated. This results in the tool gouging the part and eventually breaking of the tool.
23. CW-119502 -- Toolpath For the specific Contour Mill operation, when the Leadin/Leadout is at the end of the entity and if the Registry Flag "EnableTangentLeadinLeadout is active and the toolpath compensation is set to 'Without compensation', then thetoolpath that gets generated is incorrect for Perpendicular Leadin/ Leadout.
24. CW-119438 CSR-22573 TechDB When using the customized TechDB for programming the specific Assembly file, the coolant defined for a particular tool does not get saved and returns to the default coolant type when reopening that Assembly file.
25. CW-119429 CSR-22584 Toolpath For the Contour Mill operation of the specific Assembly file, when the Lead-In angle is set to '0' degrees within the Bottom Finish dialog box, the Lead-In move of the toolpath gouges the part even when the Gouge check option is enabled.
26. CW-119194 CSR-22499 Help In UPG Help documentation, some of the Probing System variables are not documented though those variables are available in UPG.
27. CW-119119 CSR-22541 VoluMill For the specific Assembly file, the VoluMill toolpath generated for its operation in CAMWorks 2022 andCAMWorks 23 SP0 versions are incorrect. The toolpath was getting generated correctly in CAMWorks 2021 version.
28. CW-119106 CSR-22501 Help In UPG Help documentation, there is an error in the spelling of a newly documented system variable.
29. CW-119096 CSR-22491 System For the specific Assembly file, when certain steps are followed, a warning message "The CAMWorks data in this model will be converted when saved." gets displayed. Ifthe "Ok" option is clicked, then the SOLIDWORKS application crashes and all the programmed CAM data is lost.
30. CW-118983 CSR-22456 Simulation For some specific Assembly files, the Toolpath Simulation's'Compare' functionality works only for the first componentof the assembly. For rest of the component parts of the assembly, this functionality doesn't work.
31. CW-118956 CSR-21731 System The feed length calculated for Pecking with canned cyclesis way higher compared to the production time.
32. CW-118912 -- API Within the macro for fetching user-defined holder, if user edits the path to the holder file and then re-runs the macro, it is observed that previous Holder file gets fetched rather than the expected holder file.
33. CW-118750 CSR-22378 CSR-22628 ShopFloor From CAMWorks 2023 version onwards, XSLT stylesheets for outputting Setup Sheets was introduced. Within the ShopFloor application, an option to open the HTML Setup Sheet output using such XSLT stylesheets needs to be provided.
34. CW-117986 CSR-22025 Toolpath Retract moves are not created for the last feature toolpath between the groups when the "Optimize between groups" option is checked with the 'Use skim plane with the clearance plane'.
35. CW-117080 CSR-21478 UIF In the Tool tree tab, enable the Tree Display option in its context menu. Two options viz. 'Node Name' and 'Tool Comment' must be made available in this menu.
36. CW-116885 CSR-21325 Toolpath For Contour Mill operations, if Ramp is used on Full radius Compensation toolpath, then it does not apply the selected retract point to the generated toolpath.
37. CW-112836 CSR-18878 Toolpath For any Mill-Turn part with Sketch plane as its top plane,Sub Spindle directions need to be reversed by checking the Reverse option for all Sub Spindle Bores to be correct.
38. CW-106720 CSR-15682 Toolpath For the specific part file, the CL data is incorrect for Combined drill hole operations.
39. CW-105426 CSR-15330 CSR-12192 Help The "Setup_Sheets_Tutorial.pdf" document needs to be updated to include the definitions related to all parameters that can be output when the Setup Sheets are generated.
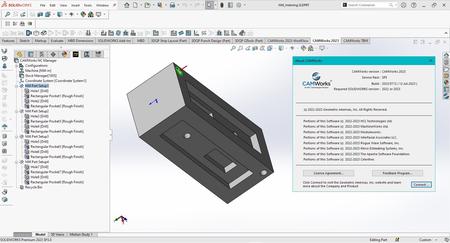
CAMWorks for SOLIDWORKSwas the first fully integrated computer-aided manufacturing (CAM) solution designed exclusively to operate in SOLIDWORKS and the first to offer knowledge-based, feature recognition, and associative machining capabilities within SOLIDWORKS. CAMWorks uses the same SOLIDWORKS geometry to generate toolpaths to ensure the part you machine is the same part you've modeled. Toolpath simulation allows users to compare "as designed" parts to "as machined" parts. The part model-to-toolpath associativity in CAMWorks increases machining productivity and lowers manufacturing costs by eliminating time-consuming CAM system rework due to design updates. CAMWorks eliminates the drudgery of CNC programming with Intelligent Machining through automation. Pioneered by Geometric Technologies, this suite of tools automates the generation of toolpaths based on a knowledge-based database. It eliminates hours of complex programming through Automatic Feature Recognition (AFR) that automatically defines prismatic machinable features, while the TechDBTM (Technology Database) defines machining operations to automatically generate accurate toolpaths at the click of a button. CAMWorks machining modules include: 2½ Axis Mill, 3 Axis Mill, Turning, Mill-Turn with 5 Axis Simultaneous Machining Support, 4/5 Axis Simultaneous Machining, and Wire EDM.
CAMWorks 2023combines the benefits of a fully integrated CAD/CAM system with advanced programming technologies such as feature-based programming, automatic feature recognition, knowledge-based machining and TechDB for storing and reusing best practices.
What's new in CAMWorks 2023 - An overview
HCLSoftwareis a division of HCL Technologies (HCL) that operates its primary software business. We develop, market, sell, and support over 30 product families in the areas of Customer Experience, Digital Solutions, Secure DevOps, Security & Automation.
Rapidgator-->Click Link PeepLink Below Here Contains Rapidgator
http://peeplink.in/6444dc2ccdeb
Uploadgig
i6uy0.setup.rar
NitroFlare
i6uy0.setup.rar
Links are Interchangeable - No Password - Single Extraction
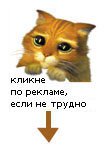