Practical Guideline To Learn 8D Problem Solving Methodology
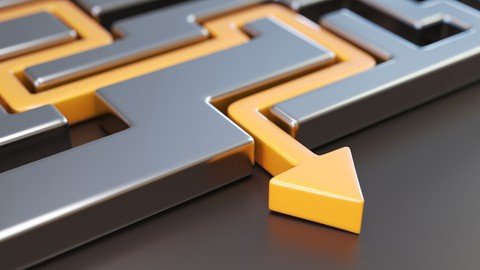
Free Download Practical Guideline To Learn 8D Problem Solving Methodology
Published 3/2023
MP4 | Video: h264, 1280x720 | Audio: AAC, 44.1 KHz
Language: English | Size: 556.02 MB | Duration: 1h 4m
Root Cause Analysis
Free Download What you'll learn
Defining each problem steps as per 8D methodology
Undestanding the root cause steps
Reaching the complete technical mindset to implement 8D Steps in project and serial manufacturing
Learning standardization and lesson learned effectively
Requirements
No specific requirements. Basic quality knowledge is enough to start this training.
Eagerness to develop skills
Description
This is a practical course for people who would like to improve their problem solving approach or New engineers/engineer candidates who are trying to learn problem solving methodology in project management and manufacturing areas.Many disciplines around the world are using 8D problem solving methodology as it is critical to achieve sustainable action, eliminate potential claims/risks and minimize claim reocccurrence.Without handling defects methodically, it will not be possible to achieve continuous improvement.-------------------------------------------------------------------------------On the professional side, you may be responsible for evaluating many 8D reports or you may be the owner to respond to your customer in a proper way.Within this course, you will also see practical case study and reconsider your current status and refresh your knowledge.Some common mistakes will guide you to focus right points directly in each 8D steps.We need to understand that 8D methodology includes team-oriented approach, but defining right team members with GEMBA analysis will surely be crucial.Problem solving is not only related to quality department, but also other departments such as supply chain, purchasing etc. need to learn how to systematically solve the critical defects. A3 report and OnePager implementations are very common, but before all of them, 8 steps must be clearly learned and the mindset must be primarily understood.-------------------------------------------------------------------------------D1: Building TeamD2: Problem DescriptionD3: Containment ActionD4: Root Cause AnalysisD5: Countermeasure/Corrective Action PlanningD6: Implementation of Corrective ActionsD7: StandardizationD8: Lesson Learned
Overview
Section 1: Introduction
Lecture 1 Intro and Scope
Section 2: D1. Building Team
Lecture 2 D1
Section 3: D2. Problem Description
Lecture 3 D2
Section 4: D3. Containment Action
Lecture 4 D3
Section 5: D4 Root Cause Analysis
Lecture 5 D4.1 Root Cause Analsis Intro
Lecture 6 D4.2 Ishikawa-Fishbone Intro
Section 6: Case Study D2 and D4
Lecture 7 Case Study D2
Lecture 8 Case Study-Starting Ishikawa-Fishbone
Lecture 9 Case Study-D4
Section 7: Case Study-Bonus-Finding Suspicious Process Step
Lecture 10 Case Study-Bonus-Finding Suspicious Process Step
Section 8: D5-D6 Corrective Actions
Lecture 11 D5-D6 Corrective Actions
Lecture 12 D5-D6 Corrective Actions-Common Mistakes
Section 9: D7. Standardization
Lecture 13 D7. Standardization
Section 10: D8. Lesson Learned
Lecture 14 D8. Lesson Learned
Section 11: Bonus-If you are not still finding the real root cause
Lecture 15 Bonus-If you are not still finding the real root cause
People who are working in industry, willing to refresh their knowledge and students who are trying to learn problem solving steps
Homepage
https://www.udemy.com/course/8d-problem-solving-r/
Rapidgator
bbvzh.P.G.T.L.8.P.S.M.rar.html
Uploadgig
bbvzh.P.G.T.L.8.P.S.M.rar
NitroFlare
bbvzh.P.G.T.L.8.P.S.M.rar
Links are Interchangeable - Single Extraction
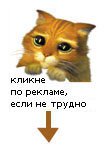